「FMEAは意味ない」「FMEAは無駄」
そんな声を耳にすることも多いですが、
「FMEAには、9割の人が知らないメリットがある」
という声も耳にすることもあります。一体どちらが正しいのでしょうか?気になりすぎたので独自のアンケート調査(n=100人)を行いました。
この記事ではFMEAが意味ないと思う人の割合から噂の真偽に決着をつけ、経験者に聞いた意味ない理由・意味ある理由(メリット)・代わりになるもの・よくある質問と回答をご紹介します。
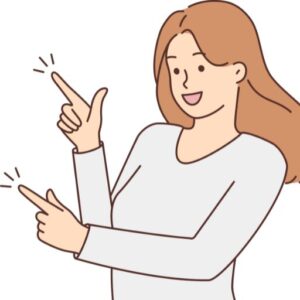
この記事の執筆・監修を担当したhanaです。
意味ないことを減らすことで人生が豊かになると信じています。
逆に、本当は意味(メリット)があることを逃さないようにすることも大切なことだと思います。
この記事は消費者庁や国民生活センター・厚生労働省の発信情報を参考にし、コンテンツ制作ポリシーに則り作成しています。
FMEAが意味ない7つの理由・口コミ・メリット
FMEAが意味ないと言われる理由は一体なんなのか、経験者100人に独自アンケート調査した結果をご紹介します。
FMEA意味ないと思う人の割合
FMEAが意味ないと思う人の割合は100人中27人です。
読者のあなたは多数派でしたか?少数派でしたか?
記事の続きで「意味ない派」「意味ある派」の理由・口コミをご紹介してるので見てみてください。
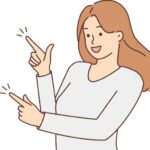
「なるほど!」と納得する意見や「それそれ!」と共感できる意見があります。
調査方法
設問:「FMEAは意味ない」と思いますか?
回答:選択方式(意味ないと思う、意味あると思う)
回答者:FMEAの経験者
回答数:100人
FMEAは意味ない派の理由・口コミ
「FMEAは意味ない」と答えた人に、その理由を聞いてみました。
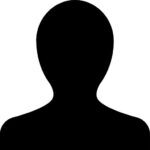
FMEAの手順が複雑で、実際のプロジェクトでは時間がなく活用できなかった。(男性)
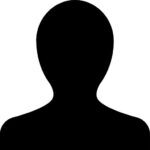
チームメンバーがFMEAの重要性を理解しておらず、協力が得られなかった。(女性)
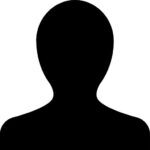
FMEAの結果が抽象的で、具体的な改善につながらなかった。(男性)
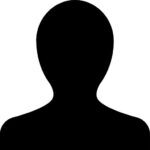
頻繁に変更が発生するプロジェクトではFMEAの更新が追いつかなかった。(女性)
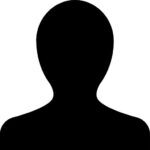
FMEAに必要なデータが不足しており、正確な分析ができなかった。(男性)
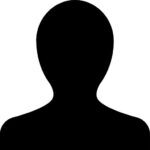
FMEAに費やすコストが高く、他の品質管理手法と比較して効果が見えなかった。(女性)
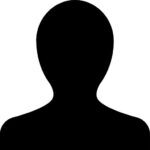
FMEAの実施に専門知識が必要で、社内に適任者がいなかった。(男性)
FMEAは意味ある理由・メリット・口コミ
「FMEAは意味ある」と答えた人に、その理由を聞いてみました。
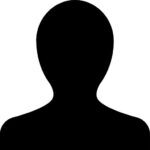
FMEAを導入してから、製品の信頼性が向上し、クレームが30%減少しました。(男性)
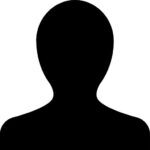
プロジェクト初期にFMEAを使うことで、潜在的な問題を早期に発見できました。(女性)
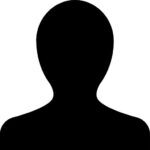
FMEAのおかげで、製造プロセスの効率が大幅に改善されました。(男性)
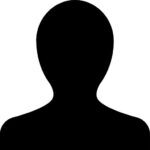
チーム全体でFMEAを実施し、コミュニケーションが円滑になりました。(女性)
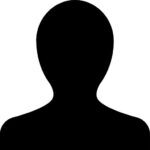
FMEAを活用してリスクを管理した結果、納期遅れがなくなりました。(男性)
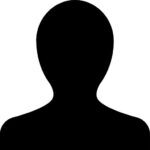
FMEAを通じて品質管理の意識が高まり、製品の品質が安定しました。(女性)
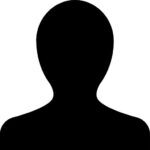
FMEAの分析により、コスト削減につながる改善点を見つけることができました。(男性)
意味ないと思う人におすすめ!FMEAの代わり
意味ある派の意見を聞いても「FMEAは意味ない」と思う人のために、FMEAの代わりになるものをご紹介します。
きっと納得できる答えが見つかるので最後までご覧ください。以下がFMEA経験者に聞いた代わりになるものです。
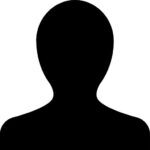
FTA(フォールトツリー解析): 新製品のトラブルシューティングにFTAを導入し、迅速に原因を特定できました。
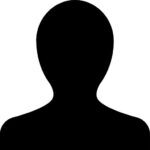
HAZOP(ハザード&オペラビリティスタディ): プロジェクトでHAZOPを使い、潜在的なリスクを事前に洗い出せました。
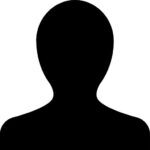
RCA(根本原因分析): 製造ラインの問題にRCAを適用し、再発防止策を確立しました。
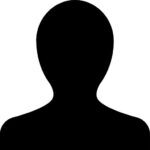
Bowtie Analysis(ボウタイ分析): 安全管理にボウタイ分析を採用し、リスクの視覚化が有効でした。
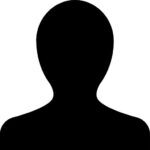
RCM(信頼性中心保全): RCMを活用して設備の保全計画を最適化し、ダウンタイムを削減できました。
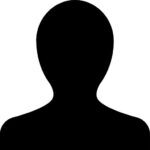
リスクマトリックス: リスクマトリックスを用いてリスク評価を簡素化し、意思決定がスムーズになりました。
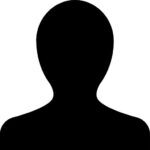
TRIZ(発明的問題解決理論): TRIZを導入して、革新的な製品改善を実現しました。
以上が代わりになるものです。
FMEAについてよくある質問【意味ない以外】
FMEAについてよくある質問をご紹介します。
FMEAとは?基本概要
FMEAは「故障モード影響分析」の略で、製品やプロセスの潜在的な故障モードを特定し、その影響を評価する手法です。リスクを未然に防ぐための重要なプロセスとして、多くの業界で採用されています。
具体的には、各故障モードの発生頻度や影響度を分析し、優先順位をつけて対策を講じます。これにより、品質向上やコスト削減が期待できます。
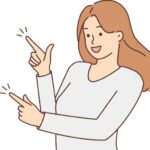
リスク管理は計画的に行うと安心感が違います。ちょっとした準備が大きなトラブルを防ぎますね。
FMEAの厳しさと対策
FMEAは詳細な分析が求められるため、時間と労力がかかることがデメリットです。綿密なデータ収集とチームの協力が成功の鍵となります。
対策としては、経験豊富なメンバーをチームに加えることや、定期的なレビューを行うことが重要です。また、専用のソフトウェアを活用することで効率化を図ることも可能です。
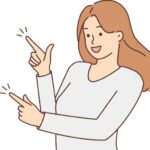
大変なプロセスも、チームで協力すれば乗り越えられます。みんなで取り組む楽しさもありますね。
FTAとFMEAの比較
FTA(フォールトツリー解析)とFMEAはどちらもリスク分析手法ですが、アプローチが異なります。FTAはトップダウン、FMEAはボトムアップの手法で進められます。
FTAは特定の事象に焦点を当て、その原因を階層的に解析します。一方、FMEAはシステム全体を対象に潜在的な故障モードを幅広く洗い出します。
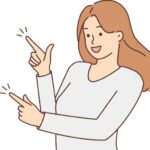
状況に応じて適切な手法を選ぶことが、効果的なリスク管理につながります。どちらも使いこなせると強力ですね。
故障モードの定義
故障モードとは、製品やシステムが正常に機能しなくなる具体的な状況や方法を指します。FMEAにおいて、この故障モードを正確に特定することが、問題解決の第一歩となります。
例えば、自動車のエンジンが過熱することが故障モードであれば、その原因や影響を詳細に分析することで、適切な対策を講じることが可能です。
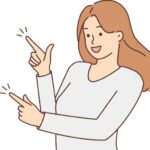
故障モードをしっかり理解することで、製品の信頼性が格段に向上しますよ。
FMEAの形骸化問題
FMEAは本来、潜在的な故障を早期に発見し対策を講じるための強力な手法ですが、形骸化してしまうケースが増えています。
形骸化の主な原因は、単なる形式的な実施に終始し、実際の分析や改善が行われないことです。その結果、FMEAの効果が薄れてしまいます。
効果的なFMEAを維持するためには、チーム全員が積極的に参加し、現実的な視点で分析を進めることが重要です。
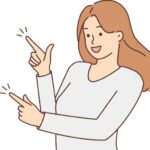
FMEAは生きた手法。定期的に見直して、常に最新の状態を保ちましょう。
故障モード一覧
FMEAを実施する際には、考えられる故障モードを網羅的にリストアップすることが大切です。故障モード一覧は、その分析の基盤となります。
この一覧には、設計上の欠陥や使用環境の変化など、様々な視点からの故障モードを含める必要があります。
具体的には、機械部品の摩耗、電子部品の過熱、ソフトウェアのバグなど、多岐にわたる項目を整理していきます。
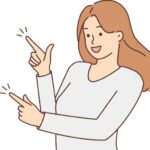
多角的な視点で故障モードを洗い出すことで、より実効性のある対策が可能になります。
故障モードの書き方
故障モードの書き方は、製品やプロセスで発生しうる問題を明確にすることが第一歩です。まず、各コンポーネントの役割と機能を理解し、それに基づいてどのような故障が考えられるかをリストアップします。
具体的な事例を挙げることで、故障の可能性や影響をより明確に把握できます。例えば、自動車のブレーキシステムでは、ブレーキパッドの摩耗や油圧の低下が故障モードとして考えられます。
また、故障モードの記載には詳細かつ具体的な情報が求められます。曖昧な表現ではなく、具体的な状況や条件を盛り込むことで、後の対策が立てやすくなります。
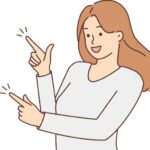
故障モードをしっかりと書き出すことで、リスク管理がスムーズになりますよ。
FMEAのやり方ガイド
FMEA(Failure Mode and Effects Analysis)のやり方は、まず製品やプロセスの各段階を詳細に分析することから始まります。
次に、各段階で発生しうる故障モードを特定し、その影響を評価します。例えば、製造工程での温度管理が不十分になると、製品の品質に影響が出る可能性があります。
その後、リスクの優先順位を決定し、重要な項目から改善策を講じていきます。
最後に、改善策の効果を検証し、必要に応じて再評価を行います。これにより、継続的な品質向上が可能となります。
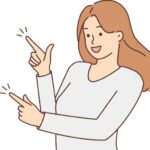
FMEAは一度やれば終わりではなく、継続的に見直すことが大切です。
FMEAとFTAの連携
FMEAとFTA(Fault Tree Analysis)の連携は、より包括的なリスク評価を実現します。
FMEAでは個々の故障モードに焦点を当てるのに対し、FTAはそれらの故障がどのように複合して重大な障害に至るかを分析します。例えば、FMEAで特定したブレーキパッドの摩耗がFTAでは他の部品との連携で大事故につながるシナリオとして検討されます。
この連携により、単独では見落としがちな原因や影響を包括的に捉えることが可能になります。
また、両手法を組み合わせることで、より効果的な対策が立案できます。FMEAで見つけたリスクをFTAで深堀りし、具体的な改善策を導出するプロセスが有効です。
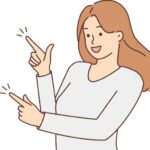
FMEAとFTAを組み合わせることで、リスク管理がより強固になります。
リスクアセスメント方法
リスクアセスメントは、プロジェクトやビジネスにおける潜在的なリスクを特定し、評価する重要なプロセスです。これにより、予期しない問題を未然に防ぐことが可能になります。
代表的な方法の一つにFMEA(故障モード影響分析)があります。FMEAは事前にリスクを洗い出し、優先順位をつける手法で、多くの企業で採用されています。
しかし、FMEAには時間とリソースが必要であり、全てのリスクを完全に網羅することは難しい場合もあります。デメリットを理解し、他のリスクアセスメント方法と併用することが効果的です。
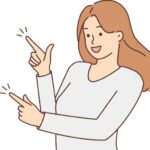
リスクをしっかり把握しておくと、安心してプロジェクトを進められますね!
【まとめ】FMEAが意味ない理由・口コミ・メリット
FMEAが意味ないと言われる理由や経験者の口コミ、実際にはメリットがあることをご紹介しました。
最後に、この記事のポイントをまとめます。
- FMEAが意味ないと思う人の割合は100人中27人です。
- FMEAが意味ないと思う人の理由は、「FMEAの手順が複雑で、実際のプロジェクトでは時間がなく活用できなかった。(男性)」です。
- FMEAが意味ないと思わなかった人の理由は、「FMEAを導入してから、製品の信頼性が向上し、クレームが30%減少しました。(男性)」です。
- FMEAの代わりのおすすめは、「FMEAの重要性を再認識するために、成功事例を共有。チーム全員が具体的な成果を目にし、モチベーションが向上しました。」です。
他にも意味ないと言われていることを独自調査した結果をご紹介しています。知らなきゃ損するメリットが隠れてることもありますので、ぜひ他の記事もチェックしてください。
コメント